Background and Situation:
The M&R Chassis Repair Shop employees all belong to a strong Union. Management has been working for decades to repair strained relations with the Union leaders amidst frequent grievances, steady drops in productivity, and increasing numbers of bad order chassis on terminal awaiting repairs. Repeated attempts to foster teamwork between union and management had not produced the intended results. Work processes were poorly defined and lacked clear methods to identify the owners of chassis before repairs began. As a result, the company repaired many chassis belonging to other companies without any means for collecting reimbursement.
Objectives:
- Implement a formal method to identify chassis owners prior to the start of repair work.
- Develop & Implement a process to estimate and schedule chassis repairs in the chassis shop
- Improve productivity and reduce the bad order chassis count by one hundred or more while minimizing the use of overtime
Results:
- Percent of available labor scheduled went from 0% to consistently over 60%.
- Schedule attainment trended from 0% to 30% on day shift and from 0% to 50% on Second shift.
- Bad order chassis count trended from approximately 440 to approximately 330
- Bad order chassis count leveled off at approximately 130
- Total annualized savings from reductions in bad order chassis numbers is $526,752.00
- Annualized ROI of 2.0: 1.0 was achieved
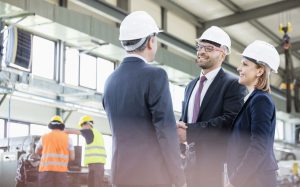