Background and Situation:
- World leading manufacturer of confectionary, foods and beverage products. Site specializes in the production and packaging of snack crackers and cereals
- Equipment and process reliability issues included:
- Reactive based maintenance culture
- Non-existent Preventive Maintenance (PM/PdM) program for new production lines
- Incomplete / obsolete Bill of Materials (BOMs) in CMMS (SAP)
- Equipment criticality not documented (based on individuals’ perceptions)
- Lack of Work Management processes to include work planning, work scheduling and work identification
- PM Backlogs out of date incomplete and not closed
- Low PM schedule attainment
- Few Planed work standards for PM completion
Objectives:
- Develop PM and BOM programs for newly installed production lines
- Develop criticality rankings for new equipment and prioritize PMs
- Develop PM schedules – Recommend frequencies
- Establish work standards for PM routines
- Develop BOMs in support of Planning & Stores
- Input PMs and BOMs into CMMS (SAP)
- Long term objective:
- Move from a reactive maintenance philosophy to a proactive philosophy thereby increasing Equipment Availability (EA) while controlling O&M costs.
Results:
- Process:
- Working with Site Management, Maintenance, Operations and Third-Party Vendors collaborated to developed PMs (mechanical, electrical and instrumentation) and BOMs for newly installed snack cracker production lines
- Established documented PM/BOM development and SAP input processes
- Developed PM criticality rankings to prioritize site efforts
- Conducted site review and sign-off of all PMs and BOMs with Site Leadership
- Established and reported weekly implementation KPIs to monitor project’s progress
- Completed PM/BOM development project on schedule and under budget
- Coached Site Leadership on process development, project management and key aspects of Work Management (i.e., Planning, Scheduling, and Work Accomplishment)
- Success of PM / BOM initiative led the Client to request additional RMG support in building and input of PMs and BOMs into Client’s CMMS (SAP) and other site Work Management support
- Performance
- Achieved 100% schedule attainment for PMs and BOMs development:
- 43 Processing systems identified
- 116 PMs developed
- 1280 BOM line items identified & criticality ranked
- 57% of BOMs input into SAP – Remaining to be completed by company personnel
- Completed development of PMs and BOMs on schedule and under budget
- Success of PM / BOM initiative lead to additional work on-site.
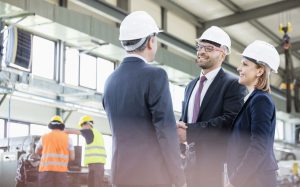