Background and Situation:
- Four generating stations representing approximately 223 MW of generation capacity for northeast Wyoming and neighboring states. Original plant built in 1967, NS 1, most recent plant Wygen 1 2001.
- 80 operations employees with contractor maintenance force of six
- Additional capacity being built to supply growing demand emphasizes need for standardized work practices.
- A mix of union and non-union employees
- Adjoining coal mine is main supplier for plants (low cost per ton for coal)
- No standard system-wide process or measures in place to proactively manage asset reliability.
Objectives:
- Establish standard planning and scheduling processes that can be used to improve plant efficiency and productivity
- Ensure PM work orders being completed at no less than 95%
- Promote a culture of accountability for results
- Establish meaningful system-wide and station measures that can be used to manage station operations more proactively
- Improve availability by .6% across all plants
- Establish system-wide steering committee to carry ownership and control of the standard system-wide process maintaining consistency and effectiveness
- Establish permanent defect elimination team (Reliability Team)
Results:
- Implemented standard daily and long-range scheduling processes, taking daily compliance to over 80% in the first three months of implementation.
- Established a Reliability Team to aid in reduction of defects and improve performance across the units.
- Implemented a standard, prioritized planning process that resulted in all scheduled jobs being planned.
- All work is now completed from work orders, verses previous practice of calling maintenance for any issue and breaking daily schedule.
- Took PM completion rates from 80% to over 95% compliance
- Established at each station a backlog of planned corrective work from zero to two weeks’ worth (based on available weekly labor at each station)
- Refined operator rounds through Action Team and improved the participation of operators in maintaining asset reliability.
- Trained and coached station leaders in using process and lagging measures, setting performance expectations and goals, and driving the work management process to achieve bottom-line results.
- Increased availability 4% YTD based on planned hours. ($1.6M)
- Cost per MW savings @ $206,258 YTD
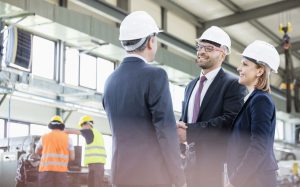