Background and Situation:
- Lack of Planning and Scheduling
- Lack of Coordination between Crafts & between Maintenance and Operations
- Poorly Defined and Documented Work Processes and Roles & Responsibilities
- Lack of Process Key Performance Indicators Driving Continuous Improvement
- Lack of Predictable Results
Objectives:
- Improve Customer Focus
- Improve Maintenance Work Predictability Through Planning and Scheduling
- Define Roles of Operations and Maintenance
- Improve Cross Craft Coordination
- Reduce Crisis Frequency
- Make all Improvements in Alignment with Site’s Loss Prevention System (LPS), and Goals for Productivity and Profitability
Results:
- Process
- Developed and implemented Work Management Processes for Backlog Management, Work ID, Planning, Scheduling, Execution, Documentation, Analysis and Measurement and Sustainability
- Improved coordination and communication between crafts and departments
- Training, field coaching and documentation to ensure sustainability including roles and responsibilities, process flows and procedures
- KPIs to monitor and track results
- Performance
- Improved Daily Schedule Attainment from less than 40% to 80% and improving
- Reduced Backlog of Maintenance Work Orders by over 42% (+3000 to approximately 1750)
- Reduced Emergency (Priority 1) work orders from over 35% to less than 10%
- Improved maintenance contractor management and control.
- Implemented contractor weekly and daily scheduling resulting in daily schedule attainment now at 75% from approximately 20%
- Improved levels of work coordination and support confidence between departments
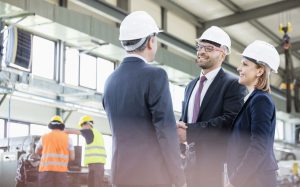