Background and Situation:
The Elkview site had a declining availability of haul trucks reducing throughput by millions of dollars annually. When truck availability dropped to its lowest point of 78%, Teck created the Accelerated Maintenance Program (AMP) to determine the root causes for this decline. The team led by the corporate improvement group engaged RMG to support their efforts using a six-sigma approach and RMG’s analysis and implementation methodologies. The data Teck collected was indicating that several “Bad Actors”, were the root cause of declining availability.
The scope of RMG’s support included:
- Analyzing, recommending, and implementing change to resolve the “Bad Actors’
- Making recommendations to site leadership on implementing changes
- Defining and recommending Organizational Structure and Reporting changes
- Leadership Development
Objectives:
- Assure alignment of the management team on a specific vision for the future state of the organization, maintenance processes, and operational performance
- Eliminate process constraints that negatively impacted truck availability
- Implement changes to enable the fleet to operate at a higher availability while maintaining required levels of reliability, safety and production
- Verify that system changes are completed, handed off to appropriate personnel and complete coaching to ensure sustainability.
- Implement improved sustainability tools, metrics usage, and habits during implementation.
- Coach leadership on behavior changes necessary to ensure more vertical and horizontal collaboration including hourly and cross functional teams (operations and maintenance)
- Create prioritization system and follow through guidelines for improving haul truck availability.
- Provide organization structure changes and role to improve communication and cost performance.
Results:
- Increased haul truck availability from 79% to 87% – $5.5M Cost Based Savings
- Improved available truck hours by 8500 hrs. annually
- Recommended changes to the organizational structure designed to achieve more realistic supervisor to employee ratios
- Improved throughput of work orders by implementing bay management techniques
- Implemented a sustained self-auditing process and process checks to capture performance outside of metrics
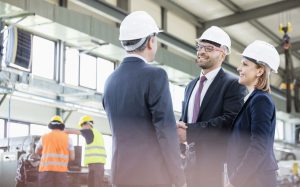